What is Porosity in Welding: Necessary Tips for Achieving Flawless Welds
Wiki Article
Porosity in Welding: Identifying Common Issues and Implementing Finest Practices for Prevention
Porosity in welding is a prevalent concern that commonly goes undetected up until it causes substantial troubles with the stability of welds. This common issue can jeopardize the strength and sturdiness of welded frameworks, positioning safety threats and causing costly rework. By recognizing the origin causes of porosity and applying efficient avoidance methods, welders can substantially improve the top quality and integrity of their welds. In this discussion, we will certainly check out the key variables adding to porosity development, examine its destructive impacts on weld efficiency, and talk about the most effective techniques that can be taken on to decrease porosity incident in welding procedures.Usual Root Causes Of Porosity
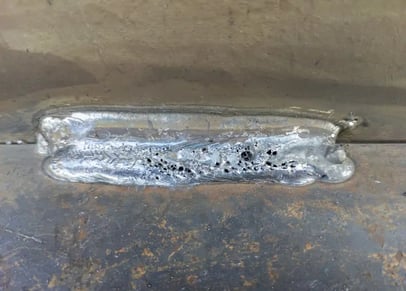
Another frequent offender behind porosity is the presence of contaminants on the surface of the base metal, such as oil, grease, or rust. When these contaminants are not effectively removed before welding, they can evaporate and come to be entraped in the weld, triggering flaws. Utilizing dirty or damp filler products can introduce impurities into the weld, adding to porosity issues. To mitigate these typical root causes of porosity, detailed cleansing of base steels, proper shielding gas option, and adherence to ideal welding specifications are important techniques in accomplishing premium, porosity-free welds.
Influence of Porosity on Weld Top Quality

The existence of porosity in welding can substantially jeopardize the structural honesty and mechanical homes of bonded joints. Porosity creates voids within the weld metal, weakening its total strength and load-bearing ability.
Among the key consequences of porosity is a decline in the weld's ductility and sturdiness. Welds with high porosity degrees tend to show lower influence toughness and decreased capacity to warp plastically prior to fracturing. This can be specifically worrying in applications where the bonded parts undergo dynamic or cyclic loading conditions. Porosity can hamper the weld's capacity to efficiently send pressures, leading to early weld failure and possible safety dangers in crucial structures. What is Porosity.
Ideal Practices for Porosity Avoidance
To boost the architectural integrity and quality of bonded joints, what specific procedures can be executed to lessen the incident of porosity throughout the welding process? Utilizing the appropriate welding method for the certain product being welded, such as adjusting the welding angle and weapon setting, can even more stop porosity. Normal assessment of welds and immediate removal of any type of concerns identified throughout the welding process are essential practices to prevent porosity and generate top notch welds.Importance of Proper Welding Techniques
Carrying out proper read the full info here welding techniques is paramount in making sure the structural honesty and high quality of welded joints, constructing upon the structure of reliable porosity avoidance steps. Too much heat can lead to increased porosity due to the entrapment of gases in the weld pool. the original source Additionally, utilizing the appropriate welding specifications, such as voltage, current, and travel speed, is important for achieving sound welds with minimal porosity.Furthermore, the selection of welding process, whether it be MIG, TIG, or stick welding, ought to line up with the specific needs of the project to ensure optimum results. Correct cleaning and preparation of the base metal, as well as choosing the ideal filler material, are likewise essential components of skilled welding methods. By sticking to these best techniques, welders can reduce the threat of porosity formation and produce top quality, structurally audio welds.
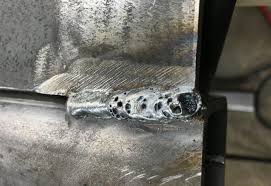
Testing and Quality Assurance Steps
Quality assurance measures play a crucial duty in confirming the honesty and dependability of bonded joints. Evaluating procedures are vital to detect and stop porosity in welding, guaranteeing the strength and durability of the end product. Non-destructive testing approaches such as ultrasonic testing, radiographic testing, and visual examination are typically utilized to recognize possible issues like porosity. These techniques enable for the analysis of weld quality without compromising the stability of the joint. What is Porosity.Post-weld examinations, on the other hand, assess the last weld for any kind of flaws, including porosity, and confirm that it fulfills defined standards. Executing a thorough quality control strategy that includes thorough testing procedures and examinations is extremely important to decreasing porosity concerns and making go sure the general quality of bonded joints.
Conclusion
Finally, porosity in welding can be a typical concern that impacts the high quality of welds. By identifying the typical sources of porosity and applying finest practices for prevention, such as proper welding methods and screening procedures, welders can make sure top quality and trusted welds. It is necessary to prioritize prevention approaches to minimize the incident of porosity and preserve the honesty of welded structures.Report this wiki page